造形加工は、金属の形状制御を目的とする基幹技術であり、鋳造、切断、圧延、積層造形など多様な工法を包含します。近年は、結晶粒微細化やヘテロ組織形成といったミクロ構造制御も、造形加工の延長線上で議論されつつあります。SDGsや脱炭素が議論される昨今、エネルギー効率や機能性材料開発の観点からも再評価が進んでいます。この記事では、加工技術の本質を見直し、将来の製造に向けた基礎をともに学ぶ道筋を紹介します。
金属加工の全体像と分類
金属加工とは、金属材料に対して力学的・熱的・化学的な処理を加え、所定の形状や機能を実現するための技術体系です。中でも造形加工は、形状制御を通じて製品構造を形成する中核的な役割を担っており、塑性加工、鋳造、積層造形などが含まれます。製品の構造や特性に直接関与するため、設計や機能面での重要性が高い加工領域です。
講師は鉄鋼業界で長く現場技術に携わってきましたが、造形加工と組織制御は決して別個のものではなく、密接に連動していることを多くの経験から実感してきました。形をつくることと、素材の性質をつくることは、常に一体で考えるべき課題です。
製錬と精錬:金属加工の出発点
金属材料の製造は、鉱石から金属を抽出する製錬、そして不純物を除去して純度を高める精錬から始まります。講師の技術者としての出発点も、まさにこの製錬・精錬技術でした。特に酸素制御による金属の品質改善は、後に「オキサイドメタラジー」として体系化しました。
オキサイドメタラジーで作られた鋼材は、北極圏の海上に立つ海洋構造物に使われました。この鋼材は、寒風吹きさらしの石油掘削プラットフォームに氷山が衝突しても耐えられるように極低温靱性に優れたものでした。
鋳造と凝固:溶融から固体へ
鋳造は、造形加工の現実的な最初の一歩です。溶融金属を鋳型に流し込み、凝固させて形状を得ます。この鋳造技術の歴史は古く、今から2000年以上も前から青銅器の鋳造が行われてきました。ただし歴史があることと制御が容易かは別物です。
この工程では、温度、冷却速度、凝固の進行方向といった物理的条件が、組織の微細構造に大きな影響を及ぼします。本講座では、講師が経験した偏析の制御や鋳造割れの話題を交えながら、鋳造や凝固の基礎が学べます。
鋳造に関する歴史エピソードはたくさんありますが、一つだけ「自由の女神」の鋳造ミス事件をご紹介しましょう。
アメリカ・ニューヨーク港内のリバティ島に立つ自由の女神像は、1876年のアメリカ独立100周年を祝して、フランスから贈られた象徴的モニュメントです。設計はギュスターヴ・エッフェル(エッフェル塔の設計者)が担当し、内部は鉄骨構造、外装には厚さ約2.4mmの銅板が使用されました。表面積は約300枚の銅板から構成され、いずれもフランスで砂型鋳造されて海を渡りました。
ところが、組み立て作業中に重大なミスが判明します。一部の銅板が、原型と逆向きに鋳造されていたのです。正確には、絵型(木型)製作段階で裏返しの形状になったまま鋳造され、それが検査・検品を通って現地に届いてしまいました。
銅板は「可鍛性」「延性」に富むとはいえ、冷間での曲げ直しには限界があります。そこで現地では、局所的に加熱しながら塑性加工を行い、元の設計通りの外形に修正する対応が取られました。鋳造という“造形の出発点”における設計ミスを、鍛造的手法という“造形の再調整”によって補った事例と言えるでしょう。
ちなみに銅板の裏表には、意匠的な浮き彫り加工(レリーフ)が施されており、裏返して使うことはできませんでした。女神様からすれば「ちょっと、私のケープ、裏返ってるじゃないの!」と苦情を申し立てたくなるような出来事だったのかもしれません。
鉄を「焼いて」部品をつくる——粉末冶金
金属造形は削って形をつくるものと思われがちですが、粉から焼いて部品を成形する技術が、実は私たちの生活の中で数多く活用されています。これが粉末冶金です。
あらかじめ配合した金属粉末を金型で圧縮成形し、高温で焼き固める焼結によって製品化するこの方法は、ギアやカムなどの複雑形状部品を切削せずに効率よく製造できます。他にも微細な形状にも対応できるMIM(金属射出成形)では、金属粉末を樹脂に混ぜて射出成形後、脱脂・焼結することで高精度な微細部品が得られます。
粉末冶金では、焼く前から仕上がりの製品が縮むことを前提に設計を行います。
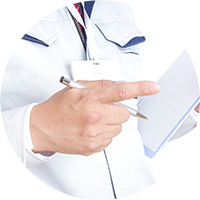
自動車、医療機器、時計など、身近な分野で粉末加工が使われています。
進化した切断技術
金属を切ると聞けば、刃物やカッターなどの工具を思い浮かべてしまいます。しかし現代の造形加工では、光・電気・水といったエネルギーが工具の役割を担っています。レーザー加工は、高エネルギーの光を一点に集中させ、金属を溶かし蒸発させて1mm単位で自在に切断します。一方、プラズマ加工は電離ガスの熱で鋼板を一気に溶断する雷の刃とも呼べる技術で、厚板などの厚物の高速切断加工ができます。そしてウォータージェット加工は、研磨剤を混ぜた超高圧水で金属を切る冷却型切断です。熱を加えないため材料の性質を保てるという特長があります。
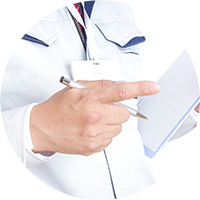
火も刃も使わずに形をつくるこの3つの技術は、ものづくりの現場を支える最前線です。
微細組織の制御と進化する造形加工
金属材料の性能を飛躍的に高めるには、形状制御だけでなく、ミクロ組織の設計が不可欠です。なかでも近年注目されるのが、ナノ組織とヘテロ組織による強度・延性制御技術です。
ナノ組織とは、結晶粒径が100ナノメートル以下の超微細構造をもつ金属材料で、粒界強化により高強度・高硬度を実現します。高圧でねじったり高圧で押し出したりして素材に非常に大きなひずみを加えて均質なナノ組織を形成します。ナノ組織化は、耐摩耗性や疲労強度が向上しますが、延性や加工性の低下が課題とされてきました。
この課題を克服するために開発が進んでいるのがヘテロ組織制御です。ヘテロ構造は、粒径や組織の異なる組織領域を意図的に共存させ、強さと粘りを両立させる技術です。異質な組織の境界に生じる強度勾配が応力を分散し、局所破壊を抑制することで、靭性や延性の向上につながります。
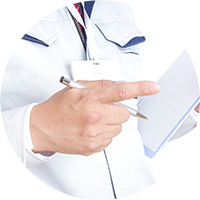
これらの組織制御技術は、形状だけでは達成できない内部構造の設計を組織制御によって行い、金属の持つ素材としての可能性をさらに広げる鍵を握っています。
終わりに
造形加工は、形状を成形する工程であると同時に、金属内部の構造を創り出す工程でもあります。講師が40年にわたり鉄鋼の製造現場で経験してきたように、鋳造や精錬から始まり、組織制御、さらには社会的要請との接点へと、造形加工はその姿を大きく変えてきました。講師が現場にいたころは、主に量産性とコストが重視されていましたが、現在ではそれに加えて、エネルギー効率、環境負荷、材料ロスの最小化といった視点が不可欠となっています。脱炭素、GX、資源循環といった社会的要請が高まる中、造形加工にも大きな転換が求められています。
SATの技術者スターター講座「造形加工」では、こうした背景にある造形技術の本質と進化に加えて、製鉄所や電気炉での鋼材の製造や粉末加工、金属の切断技術、ナノ組織の基本から応用について、講師の実務経験を踏まえて、講義の中で具体的にお伝えしたいと考えています。