塑性加工は、金属を変形させて形を作る最も基本的で汎用性の高い加工技術です。自動車の車体から電子機器の筐体に至るまで、あらゆる工業製品の構造物にこの技術が用いられています。
本記事では、塑性加工の中でも特に身近な「板金加工」と耳慣れないが現場に役立つ「トライボロジー」に焦点を当て、その仕組みと応用範囲を分かりやすく解説します。加工技術の基本を見直したい方、製造現場の理解を深めたい方に最適な内容です。
目次
塑性加工を学ぶ意義とメリット
鉄鋼製造現場の第一線で40年間技術者として働いてきた筆者が実感している経験とメリットをご紹介します。
製造技術の理解が深まる
金属加工の主流を占める塑性加工の基本を理解することができます。図面・設計から製品完成までの流れを把握でき、製造現場における作業の行動理由や目的を的確に捉えることが可能となります。金属加工の分野には塑性加工の他に除去、接合、表面加工がありますが、最も汎用性が高く応用が効くのが塑性加工です。
幅広い業種で活用可能な知識
塑性加工は、自動車、エネルギー、建設、精密機器など多様な分野で共通して用いられる技術であり、知識の習得によって業種を問わず応用が利きます。大きなものは横浜ランドマークタワーを支える極厚丸鋼管の塑性加工から自動車の部品の精密加工まで塑性加工の知識が役立ちました。
業務の選択肢が広がる
加工現場だけでなく、設計・品質管理・営業技術・保全業務など、関連部門でも塑性加工の知識は有用です。職域を超えた理解により、業務の幅が広がります。全ての職を経験してきた筆者を支えてくれたのは、塑性加工の知識でした。塑性加工用語を盛り込むことで、仕事相手へのプレゼンテーションの訴求効果は抜群です。
国際的な技術基盤への理解
日本の金属加工技術は、品質・精度の面で国際的にも高い評価を受けています。グローバルな製造拠点での適用にも対応可能な知識となります。中国とインドの製造現場の技術指導には塑性加工の技術が欠かせません。言葉は違えども塑性加工を図に書いて示すことで、相手の理解が格段に広がりました。
将来的な社会課題への対応力
EV、再生可能エネルギー、資源循環など、今後の持続可能な社会を支える技術においても、高性能な金属加工技術が不可欠です。
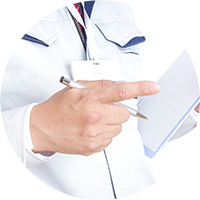
ここからは、講義をお聞きの皆さんの世界です。ぜひ塑性加工の知識を活用して、自分だけの技術体験を切り開いてください。
金属加工の主な種類
金属加工は、大きく以下のような分類に分けられます。
- 塑性加工:材料に圧力を加えて変形させる加工技術です。プレス加工や鍛造などに用いられます。
- 除去加工:材料の一部を削り取ることで形状を作る加工技術です。切削、研削、放電加工などがあります。
- 接合加工:複数の金属部品を結合する加工技術です。溶接、ろう付けなどが含まれます。
- 表面処理:耐食性や外観、摩耗性などを向上させる加工です。メッキ、塗装、コーティングの技術です。
これらの加工は、目的とする製品特性、コスト、精度、量産性に応じて適切に選定されます。
トライボロジー(摩擦・摩耗・潤滑の工学)
トライボロジーとは、摩擦、摩耗、潤滑に関する科学・工学を指します。塑性加工現場では、工具や金型と素材との接触によって発生する摩擦や摩耗が問題になります。製造現場で発生し、生産効率や製品品質、設備の維持メンテナンスに大きな影響を及ぼします。
適切な潤滑剤の使用、表面処理技術の導入、または加工材料選定の工夫など、トライボロジーの観点からの改善が、加工プロセス全体の安定性と耐久性向上に寄与します。
トライボロジーを学ぶことのメリット
金型や工具の寿命を伸ばせる
摩耗や焼き付きの原因を理解することで、適切な潤滑材や表面処理を選定でき、工具・金型の劣化を抑える対策が可能となります。これにより交換頻度の低減とコスト削減が期待できます。
加工品質の安定につながる
摩擦や摩耗のコントロールにより、バリ・寸法不良・表面粗さなどの品質ばらつきを抑制できます。特に微細加工や高精度部品においては、トライボロジーの知識が製品完成度に直結します。プレス加工の寒い朝の始業時に発生する加工不良などはトライボロジーの知識なくしては語れません。
設備トラブルの予防ができる
異常摩耗や潤滑不足によるトラブルの兆候を早期に判断でき、未然の対処が可能になります。現場保全力の強化にもつながります。
潤滑材やコーティングの選定力が向上する
加工条件や材料特性に応じて、適切な潤滑剤(油性・水溶性・固体潤滑)や表面処理(TiN、DLCなど)を選択する知識力が身につきます。これは現場改善や新規立上げにおいて必ず皆さんのお役に立つと考えます。
生産効率とコストの両立が図れる
摩擦損失の最小化と工具寿命延長により、ライン停止やロスが減り、稼働率向上とコストダウンの両立が可能となります。
素材・加工技術への理解が深まる
摩擦・摩耗のメカニズムは、素材の硬さ・靭性・表面状態と密接に関わっており、素材選定や加工法の根拠理解にも役立ちます。
研究・開発における競争力となる
近年はEV・高機能材料・環境対応型潤滑技術の分野で、トライボロジーの知識は新製品開発・技術提案の要素技術として注目されています。
プレス加工におけるトライボロジーの活用事例
プレス加工におけるトライボロジーの具体的な活用事例を筆者が体験の中からいくつかご紹介します。現場の実務にトライボロジーの理解がどのように活かされるかを明確にします。
金型の焼き付き防止対策
高張力鋼板(ハイテン)をプレス加工する際、加工熱と摩擦により金型表面が焼き付き、ワーク表面に傷や打痕が発生する現象が起こります。トライボロジー的アプローチとして、潤滑剤を従来の油性から高圧対応の固体潤滑フィルムに変更しました。さらに金型表面に硬質のDLC(ダイヤモンドライクカーボン)コーティングを施したところ焼きつきはなくなりました。この結果、加工材表面の品質安定と、金型寿命が延長しました。
スプリングバック(戻り)対策における摩擦管理
曲げ加工後の形状が設計値よりもずれる「スプリングバック」現象が発生し、後工程での手直しや再調整が必要でした。そこでトライボロジー的アプローチを試みました。摩擦係数を安定させる潤滑剤を選定し、条件を一定に保つために表面粗さや金型の摩耗による摩擦変動を管理する定期点検体制を導入しました。すると曲げ角度のばらつきが減少し、歩留まりが向上しました。さらに再調整工程を省くことができて作業工数の短縮につながりました。
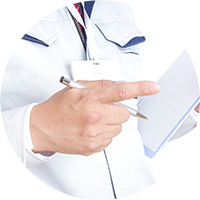
これらの事例は、トライボロジーが品質向上・生産性改善・コスト低減に効果があることを示します。特にプレス加工では、「潤滑・摩耗・摩擦」は生産の成否を左右する重要要素であり、現場における利用価値は極めて高いと自信を持っていえます。
板金加工とプレス加工
板金加工とプレス加工の特徴
板金加工:金属板(主に厚さ6mm以下)を切断、曲げ、穴あけなどによって立体的な部品に加工する方法です。多品種少量生産に適しており、比較的柔軟な対応が可能です。
プレス加工:プレス機と金型を用いて金属を高圧で変形させる加工です。大量生産に適しており、高精度かつ高速な製造が可能です。自動車や家電部品などで広く利用されています。
板金加工を学ぶことで塑性加工の理解が深まる理由
金属の変形挙動を実体験として理解できる
曲げや引張りなど、力を加えた際の金属の伸び・戻り(スプリングバック)を現場で観察できます。
加工条件と成形結果の関係を把握できる
材料の厚み・曲げ角度・工具形状によって結果がどう変化するかを実践的に学べます。
塑性加工における応力と変形の関係が体感できる
座屈や割れなど、限界成形性の理解が深まります。
工具(パンチ・ダイ)や金具設計の基本が身につく
加工精度や再現性に直結する、塑性加工全般に共通の設計思想が理解できます。
加工中の材料流動と摩擦の影響を学べる
トライボロジーの初歩(潤滑の重要性など)も自然と学習に含まれます。
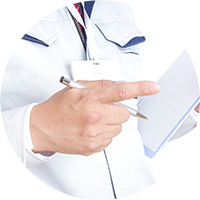
このように、板金加工は塑性加工の「実践的な入門」として非常に有効です。
板金加工に使われる主な加工法と設備
加工法 | 説明 | 主な使用設備 |
せん断加工 | 板を直線や曲線で切断する | シャーリングマシン、タレットパンチプレス |
曲げ加工 | 一定角度に板を変形させる | ベンディングマシン(ブレーキプレス) |
絞り加工 | 板を深く絞り、容器状に成形する | 油圧プレス、メカニカルプレス |
レーザー加工 | 非接触で精密に切断・穴あけを行う | ファイバーレーザー加工機 |
スポット溶接 | 板同士を局所的に接合する | スポット溶接機 |
実はこんなところにも板金加工
板金加工は、日常生活に欠かせない多くの製品に使用されています。
製品 | 材料 | 板金加工方法 |
エアコンや冷蔵庫の外装カバー | 冷延鋼板 | 曲げ、タップ穴あけ、粉体塗装 |
自動車のフロアパネルやブランケット | 高張力鋼板(ハイテン) | 曲げ、穴あけ、スポット溶接 |
パソコン筐体や制御盤 | アルミニウム、SUS304 | レーザー切断、タッピング、ベンダー曲げ |
エレベーター操作パネル、駅の券売機 | ステンレス(ヘアライン仕上げ) | タレットパンチ、エッチング、曲げ |
もっと詳しく学ぶためには
塑性加工は、製造業のあらゆる分野で必要とされる基礎技術です。加工作業自体の理解はもちろんのこと、トライボロジーのような工学的知見を含めた広範な理解が、現場力と技術対応力の向上につながります。業務の中で日々関わる金属加工技術を、体系的に学ぶことは、今後のキャリア形成にも大いに役立つものです。ぜひ、「塑性加工講座」で基本的な技術を学んでください。