こんにちは。H.Tと申します。
私は、品質工学・品質管理・技術開発マネジメントに携わってきました。
自己紹介を兼ねて、特に日本と米国の製造業における組織力とイノベーションの重要性について、私の領域での考えをお伝えします。
まずは私のこれまでのキャリアから、品質工学との歩みをご紹介します。
目次
プロフィールについて
まずは私の略歴と業績、著書について紹介いたします。
H.T氏のプロフィールをより詳細に知りたい方はこちらからアクセスください。
略歴
- 1987年 ㈱リコー入社
光ディスクの製品に従事 - 1989年 ㈱ニコン入社
新規事業開発部門に配属し、光磁気ディスクの技術開発に従事
品質工学を活用し、自社独自技術による製品の事業化に成功 - 1997年 富士通㈱ 入社
ストレージプロダクト部門に配属し、磁気ディスク、光磁気ディスクの製品設計に従事
2004年より本社部門のマネジャーとしてグループ全体への品質工学推進に従事 - 2007年 ㈱リコー入社
本社スタッフ部門のマネジャーとして品質技術の開発、推進、人財育成に従事
2021年 定年退職 - 2008年より 東京工業大学 非常勤講師
- 2021年より 現職での講演およびコンサルティング活動を開始
業績
- 2003年 品質工学会 論文賞受賞
- 2004年 品質工学会 発表賞受賞
- 2015年 第44年度 品質管理学会 品質技術賞 受賞
- 2018年 品質管理の国際大会”QMOD”にてBest Paper Awardを受賞
- 博士(工学)、品質管理検定1級
著書
- 「基礎から学ぶ品質工学」(共著)日本規格協会
- 「タグチメソッドによる技術開発~基本機能を探索できるCS-T法~」日科技連出版社
- 「日本製造業復活のための技術開発とマネジメント」(共著)日本規格協会
今も昔も変わらない品質工学の有効性
かつてJapan as No.1と言われていた頃の日本製造業は、顧客の顕在ニーズを充足しながら壊れないという意味での高品質な製品を提供することで事業を成長させてきました。
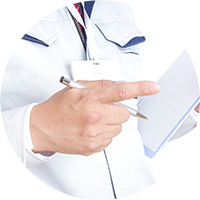
その成長の原動力は、日本独自に構築したSQC(統計的品質管理)、品質工学、QFD(品質機能展開)などの管理技術の活用です。
顧客のニーズを可視化するQFD、ロバスト性を確保する品質工学などの技法の有効性は今後も変わりません。
しかしながら顕在ニーズを充足し、かつ市場で壊れない製品を提供するだけでは事業を成長させることが困難な時代となりました。
事業を成長させるためには、お客様の期待を超える感動品質の実現が必須です。潜在ニーズを含む感動品質を備えた製品を継続的に提供することが事業を成長させる原動力となったのです。
振り返るとJapan as No.1と言われた1990年代以降、多くの日本企業は現状維持の経営を続けてきたのだと思います。現状維持は失敗の危険性を伴うチャレンジをしなくて良いので、ある意味では居心地が良いとも言えます。
しかし、グローバル視点に立つとチャレンジしない現状維持では現状を維持することすらできないことがわかります。かつては世界トップクラスであった労働生産性がOECD加盟国で29位(※2020年)まで後退してしまいました。

上位は欧米諸国が占めています。日本の労働生産性は米国の約半分まで相対的に低下してしまったのです。
成長以前の欧米企業の組織力
欧米企業が成長した要因の一つは、1980年代以降に世界トップの競争力を実現した日本企業から真摯に学んだことです。
欧米が学んだことの一つが、前述したSQC、品質工学、QFDなどの技法の活用です。技法の活用自体は日本企業を表面的に観察すれば事実として把握できますが、技法の活用だけでは日本には追い付かないという認識を持っていたところが欧米のすごさなのです。
日常業務で各技術者が技法を活用し、業務の改善を継続することが企業の競争力を維持する手段であることは間違いありません。
しかし、日常業務の改善だけでは新規事業への参入などの現状打破はできません。現状打破のブレークスルーを実現するためには組織力が必須です。
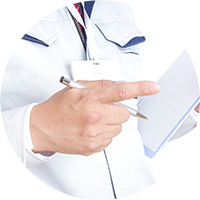
組織やチームは個人の力の総和をはるかに超える総合力を実現する手段です。この組織力の実現が欧米企業の課題であることを彼ら彼女らが認識したのです。
1990年代に米国のある製造業企業を訪問したことがあります。そこでの技術者の働き方を見て、このやり方では米国企業は絶対に日本には勝てないと思いました。
個々の技術者の知識レベルは日本の技術者よりも高いくらいなのです。博士号を持っている方もいて、とても優秀なのですが、各技術者が自分の個室の中にいて横の連絡がないのです。
さらには、製造現場で日々問題が発生していても我関せずという態度なのです。当時の日本企業では考えられないことでした。
DFSS(Design For Six Sigma)考案というブレークスルー
このような個人主義文化の欧米企業で、いかに組織力を実現するかが大きな課題です。
トップがスローガンのように「チームワークを実現せよ」などとメッセージを発信しても現場は変わりません。技法活用の効果は理屈で納得できますが、文化を変えることは容易ではありません。
そこで欧米ではDFSS(Design For Six Sigma)などの仕組みを考案したのです。
DFSSでは技術開発のプロセスを定義しています。DFSSの中にQFDや品質工学などの日本発の技法が位置付けられています。全体の仕組みの中に技法を位置付けることで技法を使う狙いがわかりやすくなります。
さらに、Pughや公理設計などの欧米が考案した技法をDFSSの仕組みに追加したのです。Pughや公理設計は言語データを扱う技法で、一人で活用するものではなくチームで発想するように仕組まれています。
個々の技法を使う理由がわかりやすく、チームワークも実現できるためイノベーションが起きやすい環境が実現しているのです。効率性と創造性を両立した技術開発プロセスの実現が欧米企業の強さの要因の一つであることは間違いありません。
DFSSは米国が中心ですが、欧州でも同様の取組みが活発です。
欧州の品質の国際大会では大学教員が発案した技術開発プロセスを自動車メーカーに入り込み実践し、論文にまとめていました。聞いてみると、品質と名が付く学問は『企業が実験室』で数社と契約していると仰っていました。
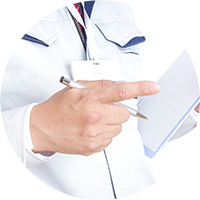
教員が大学の外に出にくい日本と違い産学連携のレベルが深いのです。産学一体で企業の技術開発プロセスや組織力を強めているのです。
日本製造業が抱えるマネジメントの困難
強い個人がチームワークで技法を活用する欧米企業に比べて日本企業の現状はどうでしょうか?
前述したように2000年代からチャレンジしない現状維持マネジメントと同時にかつての欧米流合理主義経営が主となり、短期志向での個人単位の成果が求められるようになりました。
また、QFDや品質工学などの技法だけではなく、TQM(Total Quality Management) のマネジメントの活用もかつてに比べて低下している印象です。
このような状況のままでは欧米並みの付加価値生産性を実現することは困難です。
個人の日常業務の改善のためのSQCなどの手法の活用と現状打破のための最新の仕組みの導入を両立することが現在の日本製造業復活の切り札となると考えております。チャレンジは必須ですが致命的な失敗は避けるべきです。
SAT PROで最新技法を学ぼう
私がSAT PROで提供できる最新技法の知見とは、本講座で紹介するCS(Causality Search)-T法やVOC創造型QFDなどの最新技法です。これらの最新技法は鬼に金棒の金棒です。
技術者である鬼が主役であるという意味もありますが、金棒は重たいので振り回すのにある程度の力が必用という意味もあります。
さらにはがんばって振り回していると力が付くという意味もあるのです。DFSSを日本流にアレンジして、これらの最新技法を取り入れた仕組みがT(technology)7です。
良い仕組みの中で鬼が金棒を持つことで無駄な試行錯誤や学びのない失敗を大幅低減できます。
これらの技法の案内にとどまらず、日本の製造業復活に向けたサジェスションとディスカッションができるのが、私のSAT PROでの講座の強みです。
戦後の焼け野原からJapan as No.1に至る成長、そして、その後の失われた30年までの日本と欧米の製造業で起きたことを振り返り、今後の日本製造業復活への指針を与えます。
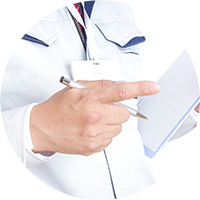
経営課題達成のためのテーマ設定、テーマを成功に導くプロセスについて、講師の失敗と成功経験に基づいた実践的な内容を解説します。